Safety, Surveillance, & CO2 Emission: The Lesser Known Applications of Drones in the Steel Industry
- Team Volar Alta
- Oct 12, 2022
- 4 min read
Updated: Sep 28, 2024
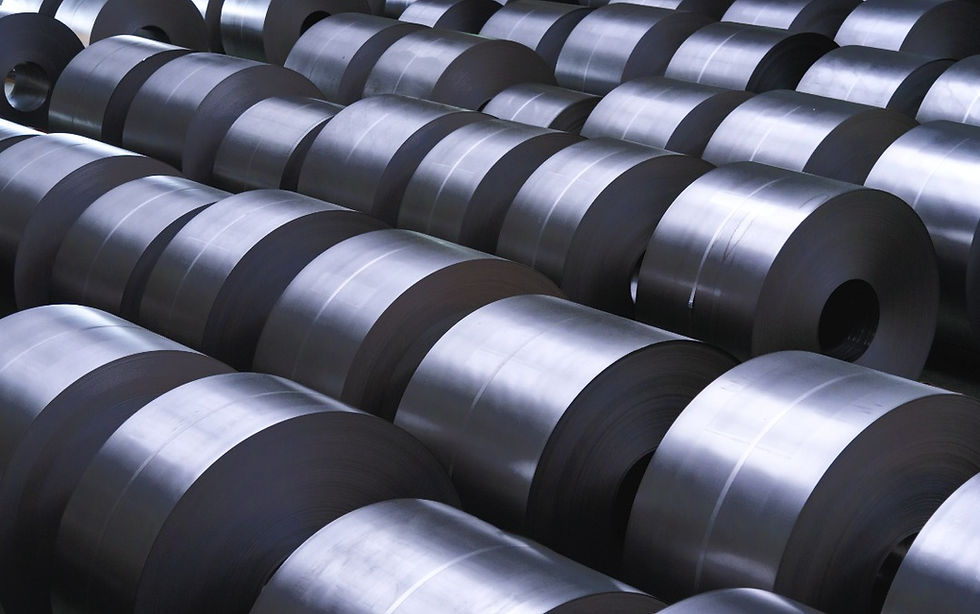
Did you know that the steel industry contributes around 2% to India's GDP, generating direct and indirect employment opportunities for six lakhs and twenty lakhs people, respectively? Despite the pandemic and lack of construction activities during lockdowns, steel production in India increased by 25.6% in FY21 as per a report. The Indian steel industry is statistically significant for the country's overall growth and development. An upward trend in this sector also boosts other related sectors.
With the growing demand, steel plants' smooth and continual functioning has become more necessary than ever before. Many experts that Volar Alta spoke to in the last two years believe that optimum operational efficiency can be achieved only through automated and digital plant inspections. Leaders are not just looking to cut costs and improve operations but also reduce carbon footprint to make their businesses sustainable and compliant.
In this blog, we aim to shed light on challenges with manual inspection and the role of drone technology in asset inspections, surveillance, and a cleaner planet.
An Overview of the Steel Industry in India
India was ranked as the second major manufacturer of crude steel globally as of October 2021, with a whopping production of 9.8 MT. The crude steel production is anticipated to hike by 18%, reaching 120 MT in FY 2022 due to a surge in demand.
To meet the market demands, steel businesses must look for sustainable solutions to make operational processes more smooth, inspections faster and environmental hazards minimum.
Why are Timely Inspections Vital for a Steel Plant?
Steel plants are inspected for safety, reliability and efficiency through timely inspections. It helps reduce risks associated with heavy machines and employees’ health on site. Besides, inspections also reduce costs by detecting defects on time before they become more expensive to fix.
Common Challenges Concerning the Manual Inspection of Steel Plants
Traditionally steel plants are inspected through manual processes. These methods put workers’ health at risk, increased downtime and impacted the environment. Workers, in steel plants, have to navigate hot machinery all the time due to the nature of work and complexities involved.
1. Workers’ health at stake:
The workers are exposed to toxic fumes, dust, and higher temperatures inside the plant that can cause respiratory problems, heart disease, and cancer. Manual inspections in the past have failed to tackle this huge problem. According to the International Labour Organization, there are more than 27 hazards that can lead to injuries and accidents in these plants. The list includes heavy lifting, noise, toxins, falls, vibration, and more.

According to a study done by the Centre for Science and Environment (CSE) in 2021, the death rate in the sector was one the highest in the world, at around 50 a year. According to another study published in NCBI in 2021, about 28% of workers experienced accidents and injuries in the last 12 months.
Frequent injuries reported were:
Cuts from sharp objects
Fractures and dislocation
Burns
Upper head injury
Arm/shoulder injury
2. The complex layout of the plant:
The layout is too multifaceted to be manually inspected as it is a massive and complicated facility. Moreover, it is hard to assess the plant with full efficiency due to a lack of visibility and accessibility in confined spaces such as furnaces, tanks, ovens, pipelines and more.
3. Difficulties in data collection:
Many variables must be considered while manually inspecting the steel plant. The data collected is not uniform and cannot be quickly processed. Therefore, some defects go unnoticed and enter the production process.
How Drones are Digitizing the Internal Inspections in Steel Industry
It should be noted that drone application in the steel and mining industry is not limited to inspections. It has been tested, across the world, from maintenance & thermal to stockpile volumetric analysis and mapping mining lands.
To overcome the aforementioned challenges, the steel industries are utilizing automated inspections through drones in the following ways:
1. Reduction in CO2 Emission:
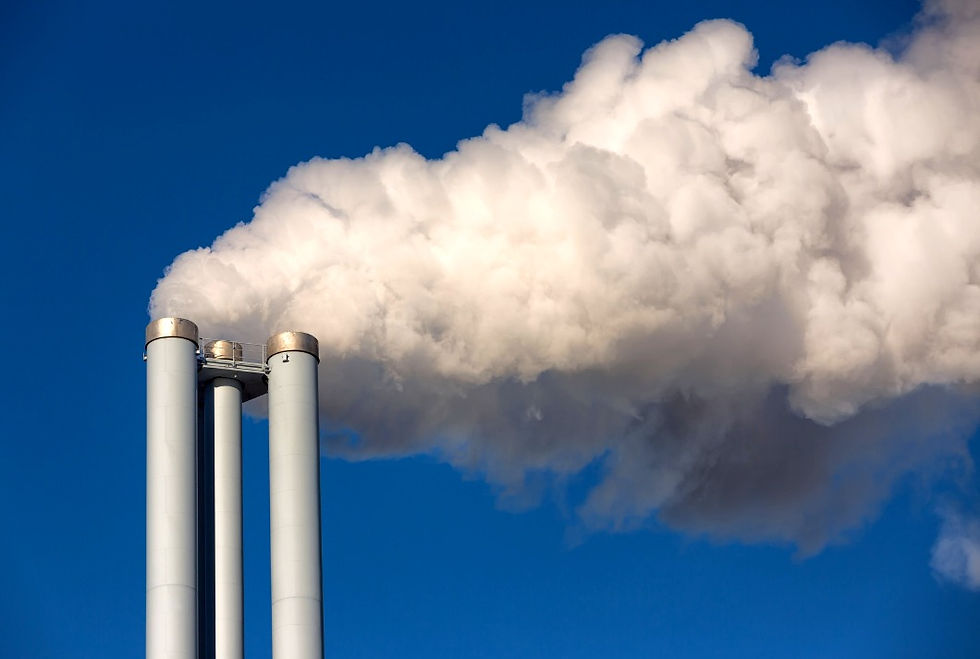
Indian steel industry's CO2 emissions are expected to reach 837 MT in the upcoming three decades compared to the current carbon footprint of 242 MT. As demand for metal goes up increasingly, estimations say that India’s steel industry will more than triple its carbon footprint by 2050.
One of the most efficient ways to reduce carbon footprint is to stop leaks and find faults and anomalies on time. Drone inspection of steel plants can help lessen CO2 emissions by finding leaks or faults that need immediate attention.
With drones’ extraordinary abilities such as multispectral cameras, they can also be used for environmental monitoring and collecting aerial multispectral imagery data. The data received here can make companies do analysis and understand what might negatively harm the environmental, botanical, and bird species.
2. Delivers data real-time:
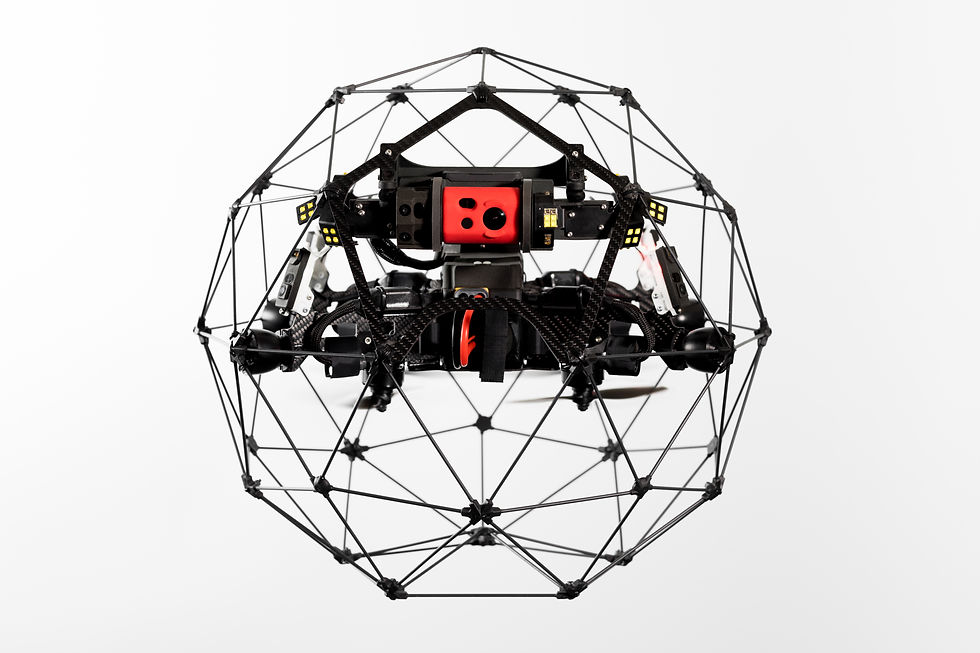
An automated internal inspection provides real-time information on plant operations and allows more accurate detection of inconsistencies or defects in the plant. Some drones like Flyability's Elios 2 also offer an insightful report mentioning the comprehensive evaluation of the plant with clear visuals.
3. Unswerving plant surveillance:
Drones provide a 360-degree view of the steel plants and have a high-resolution camera that captures detailed images for inspection purposes. Elios 2 by Flyability is a drone with a thermal camera and a 4K recording system for state-of-the-art surveillance.
4. Thermal monitoring

With thermal sensors, companies can track the heat and temperature of various assets in steel plants such as detecting roof damages before they cause leaks. In cases where there is an existing leak inside the equipment, drones with thermal cameras can generate a humidity profile of the roof structure by tracking the hidden flow of the water and identify the external point of leakage.
5. Ensuring the safety of workers and site:
Drones facilitate inspections without any risk to human life. They also aid in averting accidents at the site by detecting the hazardous issues with the steel plant at an early stage.
6. Seamless navigation and accessibility:
The automated internal inspection provides a clearer picture of what is going on in the plant. The drones have an excellent navigation system, allowing them to transverse seamlessly in the narrowest and most inaccessible spaces. It results in a high-precision assessment of the plant’s condition.
Conclusion
Manual inspection of steel plants is a time-consuming and error-prone process. That is when the drone application comes to the rescue. Drones are becoming a top-notch tool for inspecting inaccessible spaces in the steel industry. They can help companies to ensure that their plants are safe and maintain efficient production with optimal safety.
Comments